The expansion of utility digital transformation driven by increasing demand for Distributed Energy Resources (DER) and growing Advanced Distribution Management System (ADMS) implementations is well documented. These systems need a digital twin. Modern utilities are now tasked with getting high-fidelity and high-quality data into their systems of record faster to feed these network-hungry operational systems. While digitalization progresses, a pervasive problem remains in almost all electric utilities: the continued use of paper in construction as-builting. We’ve learned that this paper-burdened legacy workflow could be more efficient, is continually challenged with data quality issues, and results in massive mapping backlogs. Despite the appetite to change, the barriers to doing so are too high, and the process remains or becomes “just the way things are done.”
This article explores why as-builting remains paper-based today, introduces a new digital construction management approach that enables a digital workflow, and presents how utilities can solve this digitalization gap through change management.
The As-Is: Digital Bookends
As-builting occurs during the Planning > Construction Execution > System of Record Closeout workflow, which manages the engineering and construction of network infrastructure and updates enterprise and operational systems. Utilities have spent decades and millions of dollars digitizing the Planning and System of Record sides of this equation, pouring investments into graphic work design (GWD), geographic information systems (GIS), enterprise asset management (EAM), work management systems (WMS) and mobile workforce management (MWFM). Enterprise GIS has established itself as the mission-critical system of record for spatial assets tasked with managing and sending spatial asset and network data to ADMS. Esri, the global leader in enterprise GIS, has responded to the need for more/better/faster data with the ArcGIS Utility Network, adding advanced network modeling capabilities.
Many top GWD vendors have followed suit, offering support for Esri’s Utility Network in their design products. Recent market activity shows that utilities focus most of their attention and budgets on adopting Esri’s Utility Network and procuring GWD tools to help drive better data into their GIS. With this approach, utilities will end up with digital bookends—digital EWAM and GWD tools on one side and digital utility GIS and ADMS on the other—with paper, disjointed processes, and siloed applications used in the middle.
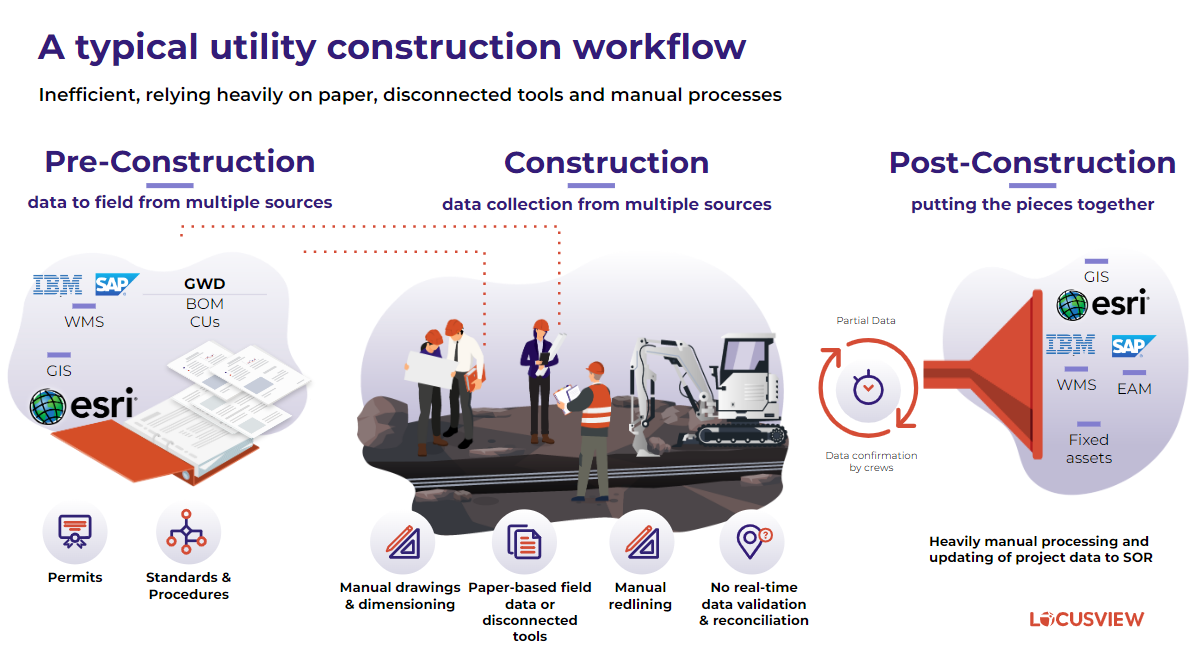
The widespread use of disjointed processes, applications, and paper during as-builting breaks this digital chain and represents the significant gap in this end-to-end workflow.
The To Be: A Digital Thread
Eliminating the paper job packet requires capturing as-built data in a way that allows data to flow seamlessly from one stage to the next, i.e., a Digital Thread. The ideal Digital Thread workflow would look something like this:
- Engineers create a digital work Order (WO) and/or a graphic work design (GWD) with a digital BOM and Compatible Units (CUs).
- Manufacturers label products with a traceability barcode that links to digital asset specification data and other essential datasets.
- Construction crews create a digital as-built by updating the digital WO BOM and/or GWD with asset data, using automated capture with barcodes and GPS.
- Construction is continually validated against the WO BOM and/or GWD with automated material validation and proposed vs. as-built summaries.
- Digital as-built data is delivered to systems of record, such as EWAM, GIS, OMS, and ADMS, for streamlined integration.
- O&M crews leverage the traceability barcode to attach inspection, performance, and repair data to the correct asset in the system of record.
- Advanced digital twin and analytical tools leverage the systems of record populated with high-quality assets.
Getting to the above, however, is a lot more challenging, as outlined in our article, High-Quality Data Is The Foundation Of A Digital Twin. Why? Because implementing and coordinating this level of change requires a holistic view, looking beyond the typical silos of engineering, supply chain, construction, and operations.
For example, utility designers and GIS techs indicate that it takes 30-90 days to get as-built information into the GIS due to disjointed processes, applications, and paper use (industry reports confirms this). While GIS seems okay with this performance, operational systems like ADMS need more/better data faster. New digital construction management solutions can cut this by 70 percent or more.
Technology Is Only Part Of The Solution
Advances in mobile applications, cloud technology, and sensors have made a user-friendly, digital as-builting a reality. Locusview’s Digital Construction Management (DCM) platform pioneers a new vision for the Planning > Construction Execution > System of Record Closeout workflow. A seamless digital job packet replaces paper job packets, as-builts, and forms. The solution adopts a mobile-first philosophy focused on the construction crew end-user persona.
If such a technology exists, the next logical question is, “Why haven’t utilities digitalized as-builting yet?” The answer to that, however, is far more complex.
Complex Problem, Personas, and Ownership
In our experience, role definition and change management are the most challenging obstacles to overcome for large utility organizations to adopt DCM workflows. Digital as-builting is a very difficult (hidden) problem that involves various personas who work in different teams, speak different “languages,” and have separate goals. There also is a lack of awareness and ownership of the as-builting process and pain points.
Getting From As-Is to To-Be Requires Change Management
Solving the digitalization gap requires coordination and integration of multiple teams and steps throughout the utility construction workflow. Utility organizations often need help seeing the bigger picture when different departments have different goals and incentives without a clear owner. Having a party that has a holistic view and that can create a unified vision is what the organization needs to tie each phase together.
At Locusview, we run Value Assessment Workshops with our customers—a robust discovery process that specifically brings together the numerous organizational subject matter experts across departments and, in some instances, operating companies. Co-moderated by a Locusview strategist and technologist, the team explores as-is construction workflows and identifies pain points. Locusview uses this information to assess potential business value gains and outlines an ideal state following a full DCM implementation.
Locusview sometimes organizes a field Proof of Concept so stakeholders can experience the technology firsthand.
The output of these workshops sets a course for organizations to change and adopt industry best practices, simplify construction workflows, and recognize the shortened time to value.
Conclusion
Utilities have spent decades and millions of dollars digitizing the EWAM, GWD and GIS sides of the Planning > Construction Execution > System of Record Closeout workflow, only to end up with a set of digital bookends. Yet the days of this legacy workflow are numbered as infrastructure construction increases, resources are scarce, and safety and compliance pressures mount. The widespread use of paper during as-builting represents the last gap in this workflow.
Utilities desperately need a better way to capture construction data and update EWAM, GIS, and ADMS quickly and easily. Bringing together the various personas under a unified vision requires a holistic view that looks beyond the typical silos of engineering, supply chain, construction, and operations supported by a proven DCM technology solution.
Our Value Assessment Workshops, domain expertise, customer experience, and pioneering technology help customers realize tangible business value more quickly.
CONTACT US TO LEARN MORE ABOUT LOCUSVIEW'S VALUE ASSESSMENT WORKSHOPS.
The expansion of utility digital transformation driven by increasing demand for Distributed Energy Resources (DER) and growing Advanced Distribution Management System (ADMS) implementations is well documented. These systems need a digital twin. Modern utilities are now tasked with getting high-fidelity and high-quality data into their systems of record faster to feed these network-hungry operational systems. While digitalization progresses, a pervasive problem remains in almost all electric utilities: the continued use of paper in construction as-builting. We’ve learned that this paper-burdened legacy workflow could be more efficient, is continually challenged with data quality issues, and results in massive mapping backlogs. Despite the appetite to change, the barriers to doing so are too high, and the process remains or becomes “just the way things are done.”
This article explores why as-builting remains paper-based today, introduces a new digital construction management approach that enables a digital workflow, and presents how utilities can solve this digitalization gap through change management.
The As-Is: Digital Bookends
As-builting occurs during the Planning > Construction Execution > System of Record Closeout workflow, which manages the engineering and construction of network infrastructure and updates enterprise and operational systems. Utilities have spent decades and millions of dollars digitizing the Planning and System of Record sides of this equation, pouring investments into graphic work design (GWD), geographic information systems (GIS), enterprise asset management (EAM), work management systems (WMS) and mobile workforce management (MWFM). Enterprise GIS has established itself as the mission-critical system of record for spatial assets tasked with managing and sending spatial asset and network data to ADMS. Esri, the global leader in enterprise GIS, has responded to the need for more/better/faster data with the ArcGIS Utility Network, adding advanced network modeling capabilities.
Many top GWD vendors have followed suit, offering support for Esri’s Utility Network in their design products. Recent market activity shows that utilities focus most of their attention and budgets on adopting Esri’s Utility Network and procuring GWD tools to help drive better data into their GIS. With this approach, utilities will end up with digital bookends—digital EWAM and GWD tools on one side and digital utility GIS and ADMS on the other—with paper, disjointed processes, and siloed applications used in the middle.
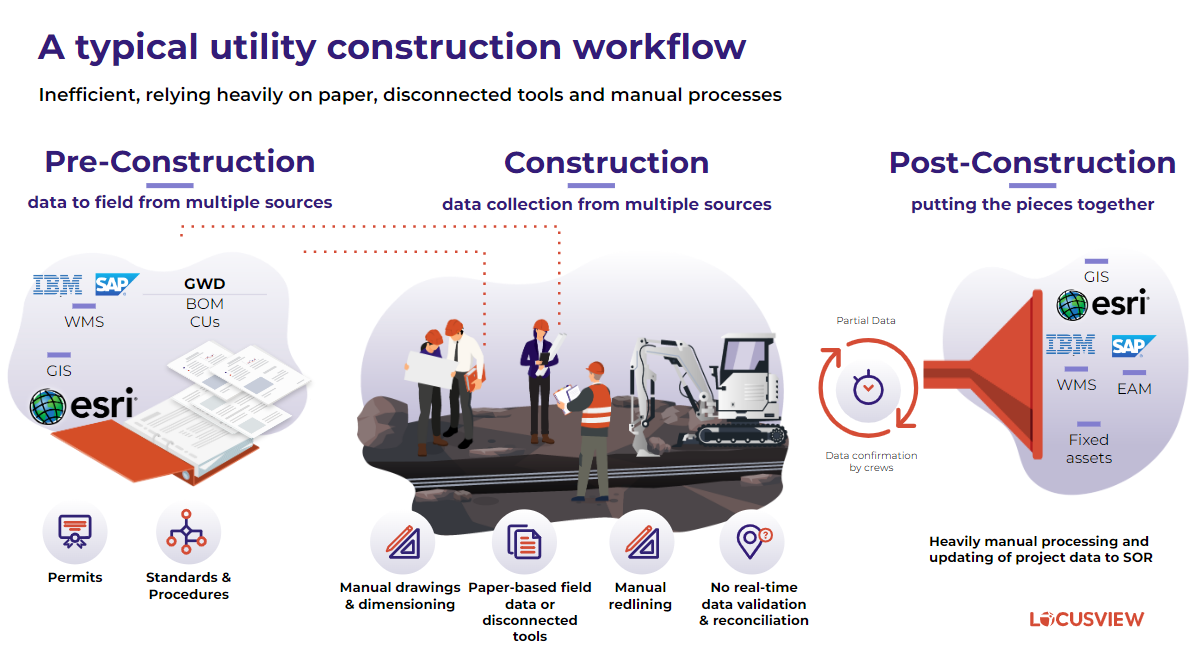
The widespread use of disjointed processes, applications, and paper during as-builting breaks this digital chain and represents the significant gap in this end-to-end workflow.
The To Be: A Digital Thread
Eliminating the paper job packet requires capturing as-built data in a way that allows data to flow seamlessly from one stage to the next, i.e., a Digital Thread. The ideal Digital Thread workflow would look something like this:
- Engineers create a digital work Order (WO) and/or a graphic work design (GWD) with a digital BOM and Compatible Units (CUs).
- Manufacturers label products with a traceability barcode that links to digital asset specification data and other essential datasets.
- Construction crews create a digital as-built by updating the digital WO BOM and/or GWD with asset data, using automated capture with barcodes and GPS.
- Construction is continually validated against the WO BOM and/or GWD with automated material validation and proposed vs. as-built summaries.
- Digital as-built data is delivered to systems of record, such as EWAM, GIS, OMS, and ADMS, for streamlined integration.
- O&M crews leverage the traceability barcode to attach inspection, performance, and repair data to the correct asset in the system of record.
- Advanced digital twin and analytical tools leverage the systems of record populated with high-quality assets.
Getting to the above, however, is a lot more challenging, as outlined in our article, High-Quality Data Is The Foundation Of A Digital Twin. Why? Because implementing and coordinating this level of change requires a holistic view, looking beyond the typical silos of engineering, supply chain, construction, and operations.
For example, utility designers and GIS techs indicate that it takes 30-90 days to get as-built information into the GIS due to disjointed processes, applications, and paper use (industry reports confirms this). While GIS seems okay with this performance, operational systems like ADMS need more/better data faster. New digital construction management solutions can cut this by 70 percent or more.
Technology Is Only Part Of The Solution
Advances in mobile applications, cloud technology, and sensors have made a user-friendly, digital as-builting a reality. Locusview’s Digital Construction Management (DCM) platform pioneers a new vision for the Planning > Construction Execution > System of Record Closeout workflow. A seamless digital job packet replaces paper job packets, as-builts, and forms. The solution adopts a mobile-first philosophy focused on the construction crew end-user persona.
If such a technology exists, the next logical question is, “Why haven’t utilities digitalized as-builting yet?” The answer to that, however, is far more complex.
Complex Problem, Personas, and Ownership
In our experience, role definition and change management are the most challenging obstacles to overcome for large utility organizations to adopt DCM workflows. Digital as-builting is a very difficult (hidden) problem that involves various personas who work in different teams, speak different “languages,” and have separate goals. There also is a lack of awareness and ownership of the as-builting process and pain points.
Getting From As-Is to To-Be Requires Change Management
Solving the digitalization gap requires coordination and integration of multiple teams and steps throughout the utility construction workflow. Utility organizations often need help seeing the bigger picture when different departments have different goals and incentives without a clear owner. Having a party that has a holistic view and that can create a unified vision is what the organization needs to tie each phase together.
At Locusview, we run Value Assessment Workshops with our customers—a robust discovery process that specifically brings together the numerous organizational subject matter experts across departments and, in some instances, operating companies. Co-moderated by a Locusview strategist and technologist, the team explores as-is construction workflows and identifies pain points. Locusview uses this information to assess potential business value gains and outlines an ideal state following a full DCM implementation.
Locusview sometimes organizes a field Proof of Concept so stakeholders can experience the technology firsthand.
The output of these workshops sets a course for organizations to change and adopt industry best practices, simplify construction workflows, and recognize the shortened time to value.
Conclusion
Utilities have spent decades and millions of dollars digitizing the EWAM, GWD and GIS sides of the Planning > Construction Execution > System of Record Closeout workflow, only to end up with a set of digital bookends. Yet the days of this legacy workflow are numbered as infrastructure construction increases, resources are scarce, and safety and compliance pressures mount. The widespread use of paper during as-builting represents the last gap in this workflow.
Utilities desperately need a better way to capture construction data and update EWAM, GIS, and ADMS quickly and easily. Bringing together the various personas under a unified vision requires a holistic view that looks beyond the typical silos of engineering, supply chain, construction, and operations supported by a proven DCM technology solution.
Our Value Assessment Workshops, domain expertise, customer experience, and pioneering technology help customers realize tangible business value more quickly.